“為什么同樣的絞線機,生產效率相差30%?” 這是某線纜廠技術主管在行業(yè)會議上提出的疑問。經過深入分析,答案直指一個常被忽視的細節(jié)——絞線機米數(shù)換算的精準度。在電線電纜制造領域,掌握米數(shù)換算公式不僅能避免原材料浪費,更直接關系到訂單交付周期與生產成本控制。
一、絞線機米數(shù)換算的核心邏輯
絞線機通過將多根單絲導體按規(guī)則絞合形成線纜,其米數(shù)計算需綜合考量線軸容量、絞合節(jié)距、導體直徑三大參數(shù)。其中,米數(shù)換算公式的本質是建立“線軸物理空間”與“線纜理論長度”的數(shù)學關系。
1. 線軸容量與線纜體積的平衡
線軸的裝載能力由公式 V=π×(R2?r2)×H 定義(R為線軸外半徑,r為內半徑,H為有效寬度)。而單根線纜體積為 v=π×(d/2)2×L(d為線徑,L為長度)。當絞合N根導體時,總長度需滿足 N×v≤V。通過變形可得基礎換算關系:
L = (R2?r2)×H / (N×d2/4)
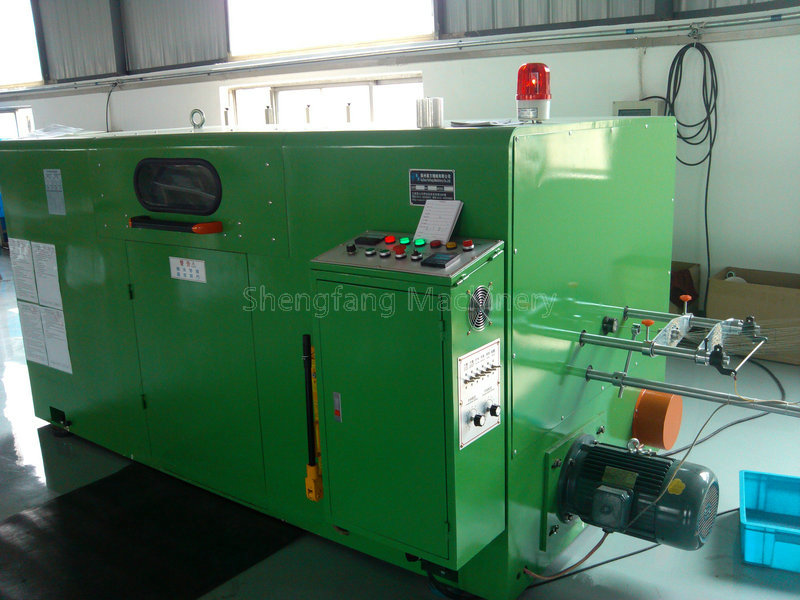
關鍵點:線軸的實際利用率通常需保留10%-15%安全余量,避免絞合過程中因張力波動導致線纜溢出。
二、影響換算精度的四大修正因子
基礎公式僅適用于理想狀態(tài),實際生產中需引入修正系數(shù)以提高精度:
修正因子 |
影響機制 |
典型調整幅度 |
絞合節(jié)距(P) |
絞合角導致導體實際長度增加 |
+3%~8% |
延伸率(ε) |
絞合張力使導體拉伸 |
+1%~5% |
填充系數(shù)(K) |
導體間隙與排列緊密度的動態(tài)變化 |
-5%~12% |
溫度膨脹(α) |
金屬導體受熱膨脹導致的線徑變化 |
±0.5%~2% |
優(yōu)化后的計算公式為:
L = [(R2?r2)×H×K] / [N×(d×(1+αΔT))2/4 × (1+P/(πD)) × (1+ε)]
(D為絞合層平均直徑)
三、實戰(zhàn)案例:如何用公式提升生產效率
某企業(yè)生產7根0.2mm銅絲絞合的線纜,原采用經驗估算法導致10%的線軸余料浪費。通過公式計算發(fā)現(xiàn):
- 關鍵參數(shù)輸入
- 線軸規(guī)格:R=150mm, r=50mm, H=200mm
- 導體參數(shù):d=0.2mm, N=7, P=12mm
- 環(huán)境條件:ΔT=15℃(銅的α=0.004/℃)
- 分步計算
- 基礎長度:L?=(1502?502)×200/(7×0.22/4)=18,285m
- 節(jié)距修正:1+12/(π×1.5)=2.546 → 修正后長度=18,285⁄2.546≈7,180m
- 溫度修正:d’=0.2×(1+0.004×15)=0.212mm → 長度再降為6,890m
- 填充系數(shù)(取K=0.88):最終L=6,890×0.88≈6,063m
- 效果驗證
實際裝載6,100m時線軸余量3%,較原先經驗值(約5,500m)提升11%裝載量,年節(jié)省銅材成本超26萬元。
四、智能換算工具的開發(fā)趨勢
傳統(tǒng)手動計算易受人為誤差影響,當前行業(yè)正朝兩個方向升級:
- 嵌入式實時計算系統(tǒng)
在絞線機PLC控制器中預裝換算程序,通過激光測徑儀、溫度傳感器自動采集d、ΔT數(shù)據(jù),動態(tài)調整參數(shù)。
- 云平臺大數(shù)據(jù)優(yōu)化
某頭部企業(yè)建立的線纜生產云平臺,已積累超過50萬組絞合數(shù)據(jù)。通過機器學習發(fā)現(xiàn):
- 當絞合節(jié)距與線徑比(P/d)處于8-12區(qū)間時,絞合效率最佳
- 銅鋁導體的填充系數(shù)差異可達7.2%
(圖示:集成傳感器與計算模塊的智能絞線機工作流程)
五、操作誤區(qū)與規(guī)避方法
- 誤區(qū)1:忽略絞合方向對長度的影響
→ 左向絞合比右向平均多耗材1.2%-1.8%,需在公式中增加方向系數(shù)μ(左向取1.015-1.018)。
- 誤區(qū)2:未考慮絕緣層厚度變化
→ 生產絕緣線纜時,需將導體直徑d替換為絕緣后外徑D_insulated,并重新計算截面積。
- 誤區(qū)3:過度追求理論極值
→ 某廠家嘗試將填充系數(shù)K提升至0.95,結果導致絞合斷線率上升4倍。建議K值不超過0.92。
TAG: